Lift Repairs – When Your Elevator Has Broken Down
At VM Elevators, we deliver expert lift repair services tailored to meet the needs of businesses and property owners across London, Essex, and the Home Counties. Whether it’s a minor fault or a critical lift breakdown, our team is ready to provide rapid, reliable solutions. We serve London, Essex, Berkshire, Buckinghamshire, Hertfordshire, Kent, Surrey, East and West Sussex, Middlesex, Oxfordshire, and Bedfordshire with 24/7 emergency support and qualified lift engineers.
Why Our Lift Repair Services Stand Out
- Efficient Repairs: Prompt service to minimise downtime.
- Coverage of all lift types: From passenger lifts to dumbwaiters and vehicle lifts.
- 24/7 Emergency Care: We’re available whenever you need us.
- Compliance Guaranteed: Repairs meet all British and European safety standards.
- Real-Time Documentation: Electronic job sheets with photos for complete transparency.
Comprehensive Lift Repairs in London, Essex & the Southeast
We provide repair services for all types of lifts:
- Passenger Lifts
- Glass and Scenic Lifts
- Goods and Service Lifts
- Platform Lifts
- Dumbwaiters
- Vehicle Transportation Lifts
- Escalators and Moving Walkways
- Mobility Lifts in Homes
What Makes Our Lift Repair Team Unique
Our engineers are DBS-checked, fully certified, and skilled in repairing lifts from top manufacturers such as Otis, TK Elevator, Orona, and Schindler. We use advanced diagnostic tools and offer a proactive approach with preventative maintenance options.
Lift Fault Diagnosis – What We Offer
- Diagnostic Services
- Electrical Repairs (control panels, safety systems)
- Mechanical Repairs (motors, doors, gearboxes)
- Software & System Support
- Safety Device Testing & Repair
Safety-First Approach to Lift Repairs at VM Elevators
We prioritise passenger safety by conducting rigorous checks on emergency systems, door mechanisms, control panels, and lift shafts. All services comply with BS EN 81 standards, SaFed guidelines, and European Directives. Our QHSE team ensures you stay up to date with compliance.
Preventative Maintenance Options
Avoid costly breakdowns with regular inspections and tailored service plans. We recommend proactive maintenance to extend the life and safety of your lifts.
Why Routine Maintenance is Important
Prevent minor lift repairs turning into costly ones with a bespoke lift maintenance contract to suit your business needs.
Having your lift routinely serviced is a legal requirement, it also ensures that your form of vertical transportation operates safely and smoothly – lessening any long-term costs, extending the time between call backs, increasing the reliability and reducing the risk of accidents incurring – all of which will ultimately prolong its lifespan.
We offer lift maintenance, dedicated care and support on lifts and escalators throughout various business sectors, including commercial, corporate, hospitality, industrial, public, real estate, residential and retail.
We work across all types of lifts, ranging from MRL, Electric, Traction, Hydraulic Passenger or Goods, Glass or Scenic lifts, platform lifts, dumb waiters, car lifts, mobility, dock leveller and scissor lifts. We also take care of escalators and moving walkways under our umbrella.
We have a variety of different maintenance contracts to suit our client’s needs. All our maintenance contracts have been approved by The Lift and Escalator Association of which we hold full membership to.
Many of our maintenance contracts also include comprehensive callouts and minor repair work, all covered under a one year warranty.
Our in-house Service team are on hand between 08.00 and 17.00 Monday – Friday, please give us a call for free on 0800 448 8615 if you have any queries you would like to discuss.
ROPES
LIGHTING
WIRING
LANDING, CALL PUSH BUTTONS & CONTROL PANELS
LIFT COMMUNICATION & ALARM FEATURES
LUBRICATION OF GUIDES, SCREWS AND SHOES
FLOOR LEVELLING
CAR ROOF TOP AND SHAFT CLEAN DOWN
DOOR CLEARANCES
CAR MOTOR
DOOR TRACKS
DOOR SAFETY DEVICES
STATUTORY LIFT INSPECTIONS
Legislative examinations and requirements should be undertaken by an external persons or third party to avoid any conflict of interests.
Inspections take place in normal circumstances and can list defects ranging from A-C. Our clients work collaboratively with us and forward through the Insurance reports upon completion so we can ensure any defects are rectified or quoted for promptly and our records are also updated with respect to time frame expectations for the next insurance inspection.
In accordance with the Lifting Operations & Lifting Equipment Regulations 1998 (LOLER), specific types of transportation that move people or goods to different floor levels are not subject to LOLER’s requirements.
Although, if the item is being used at work for example an escalator and/or moving walkway, then the Provision and Use of Work Equipment Regulations 1998 (PUWER), does come into power.
SAFETY
It is critical that building owners educate users on how to use the vertical transportation correctly. At VM Elevators we support and inform all our clients on how they can prevent breakdowns in the first instance.
More often than not breakdowns stem from misuse, examples can be overloading the lift threshold, knocking the door contacts out of place, or even tampering with the equipment.
Our Service and Repairs team train our clients in what to watch out for.
All lift and escalator equipment should be labelled with the appropriate safety signage, signaling areas off limit to unauthorised persons.
Call us for free on 0800 448 8615 to speak to one of our expert management team, or submit an enquiry to find our how we can help you elevate your business today.
24/7 Emergency Support
For contracted customers, VM Elevators provides 24/7 emergency lift callout services. Whether it’s a breakdown, a passenger trap, or a critical fault, our engineers are on standby to respond without delay. We specialise in fast, efficient solutions, including urgent lift repairs, which are essential in commercial and public environments where downtime must be minimised. Backed by CHAS ELITE accreditation, we deliver consistently safety-compliant lift repairs across London, Essex, and the Home Counties.
Engineer Excellence and Transparent Reporting
All our engineers wear VM Elevators uniforms, badges, and PPE. We complete digital job reports in real-time and include signed log cards and photographs for accountability.
Sector-Specific Lift Repair Services
- Commercial Properties
- Hotels and Leisure Venues
- Hospitals and Healthcare
- Apartments and Housing
- Educational Institutions
- Warehouses and Logistics Facilities
Partner with VM Elevators for Lift Services
- Sector-specific knowledge
- Customised maintenance and repair plans
- London, Essex & Home Counties 24/7 customer service
- Scalable solutions for single or multi-site operations
Contact VM Elevators for Expert Lift Repairs
Need fast, compliant lift repairs? Get in touch with VM Elevators today for expert lift repair services across London, Essex, and the Home Counties. Let us restore your lifts to full operation—safely and efficiently.
TRUSTED BY
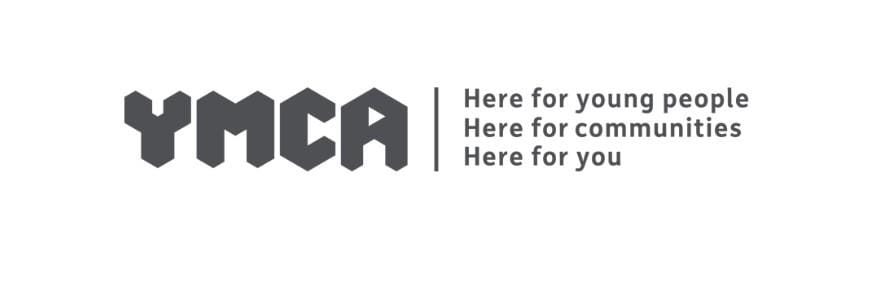
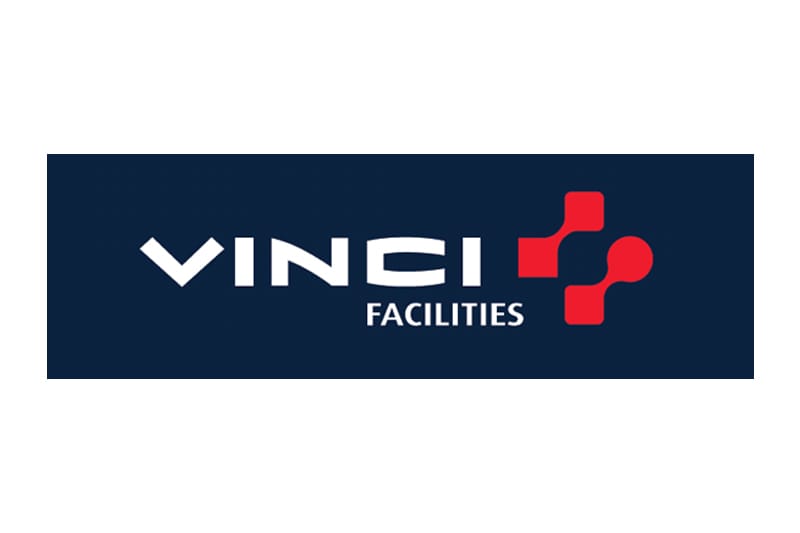
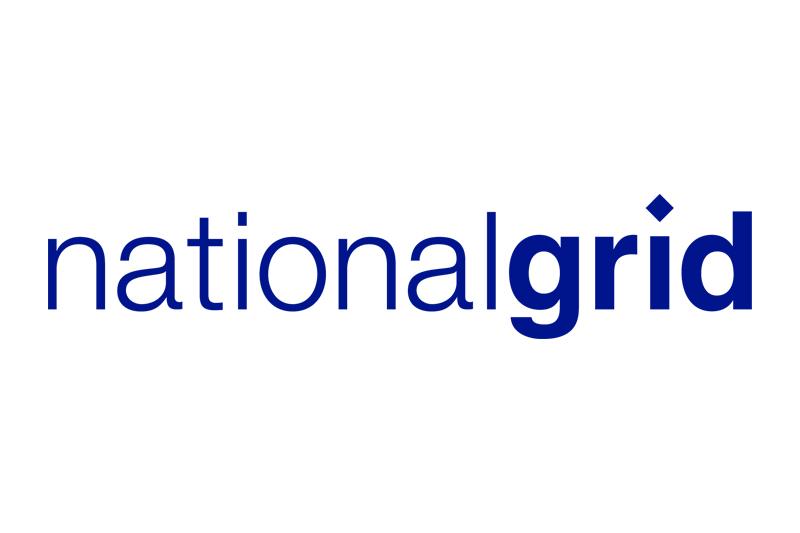
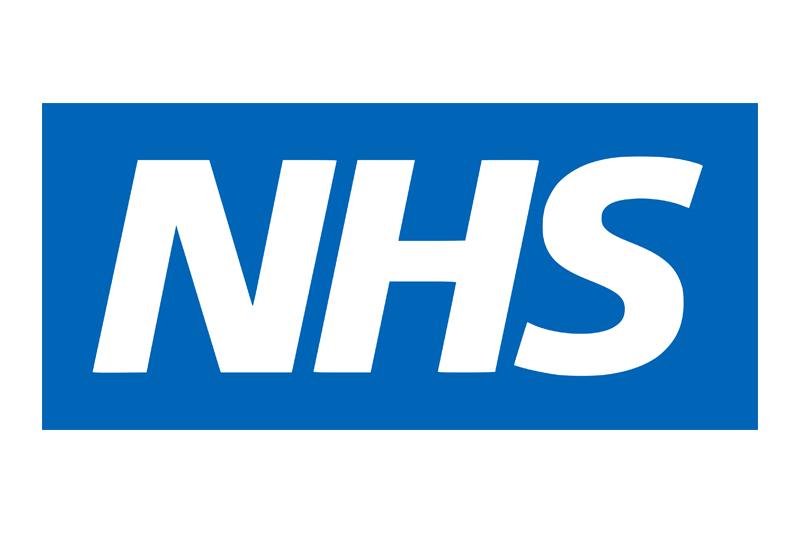
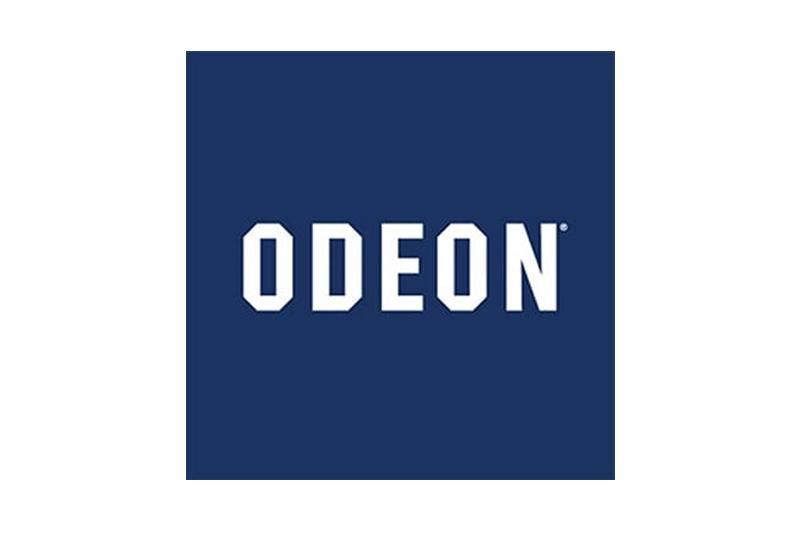
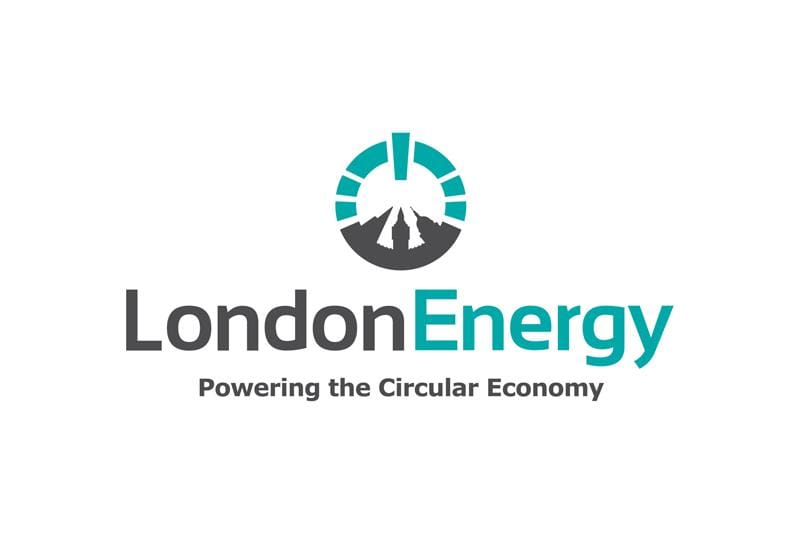
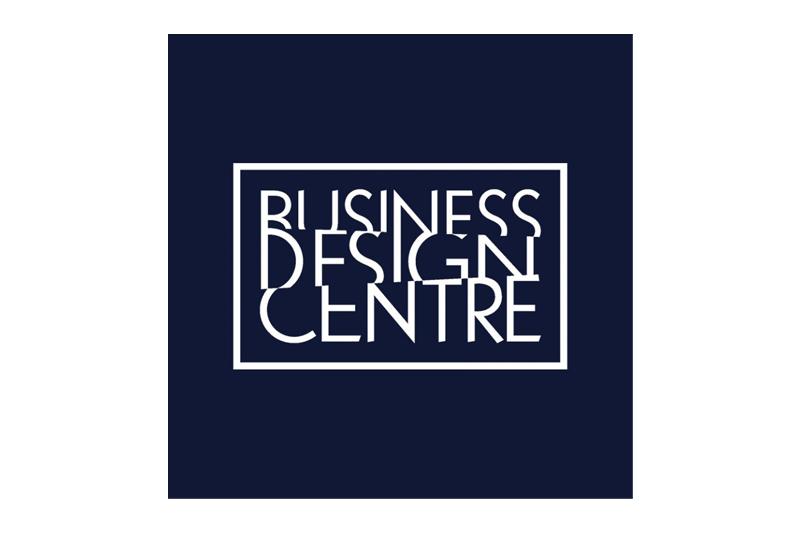
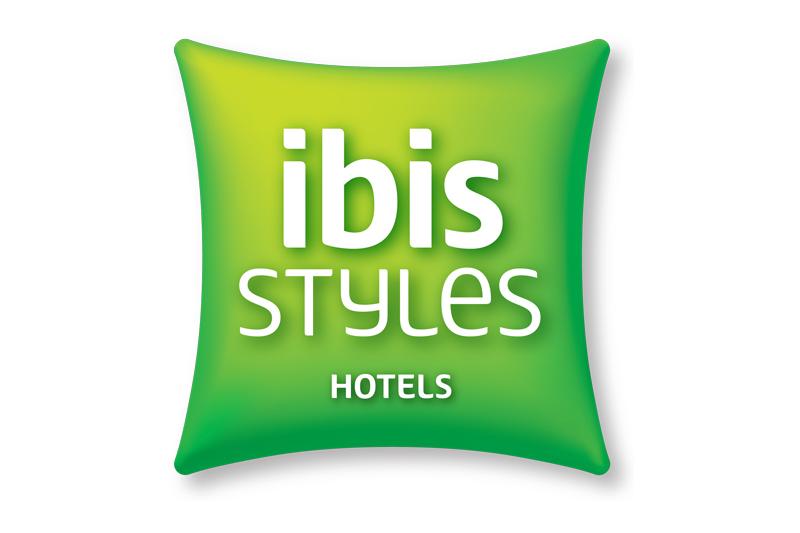
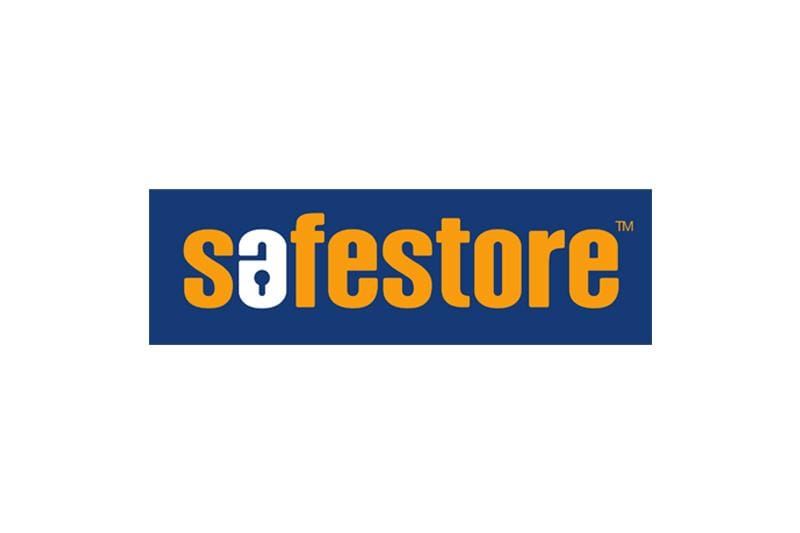
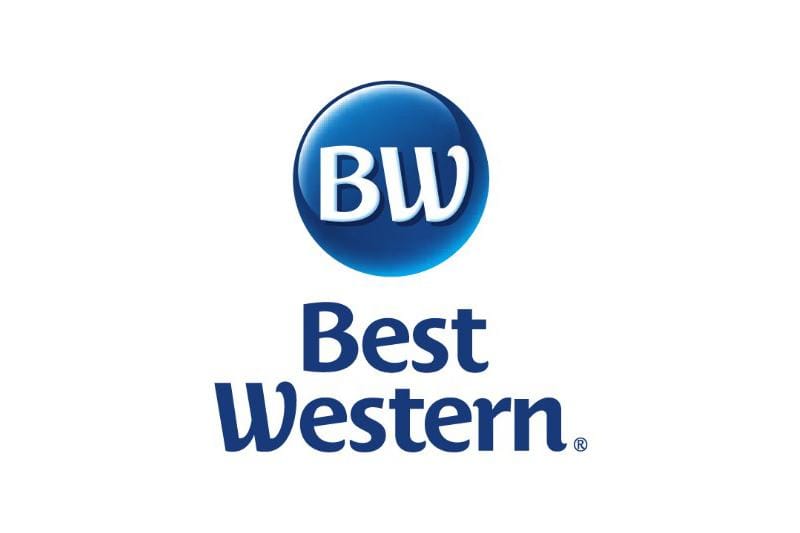
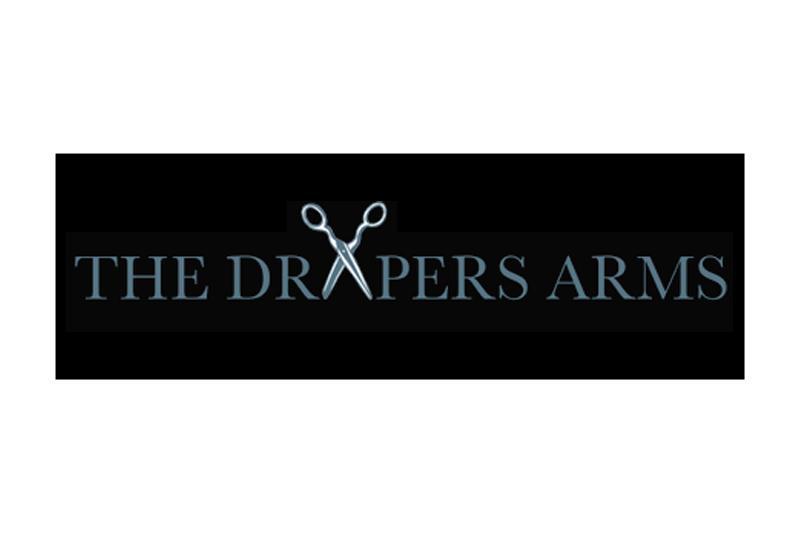
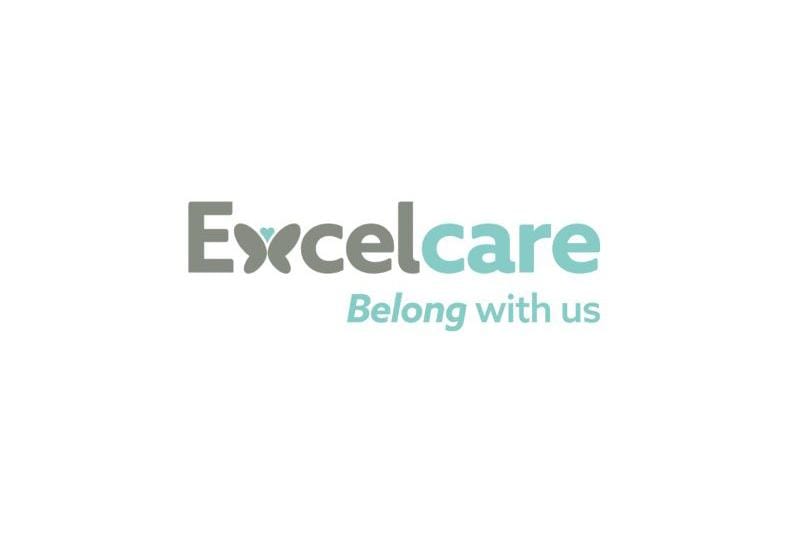
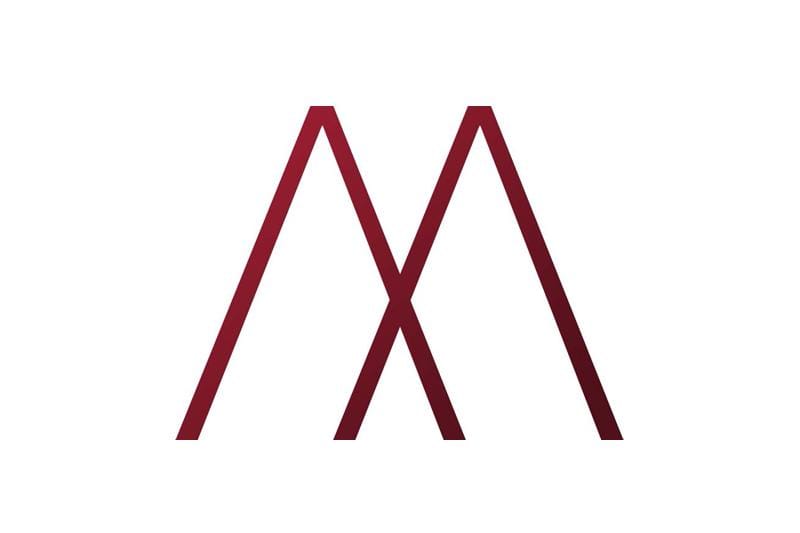
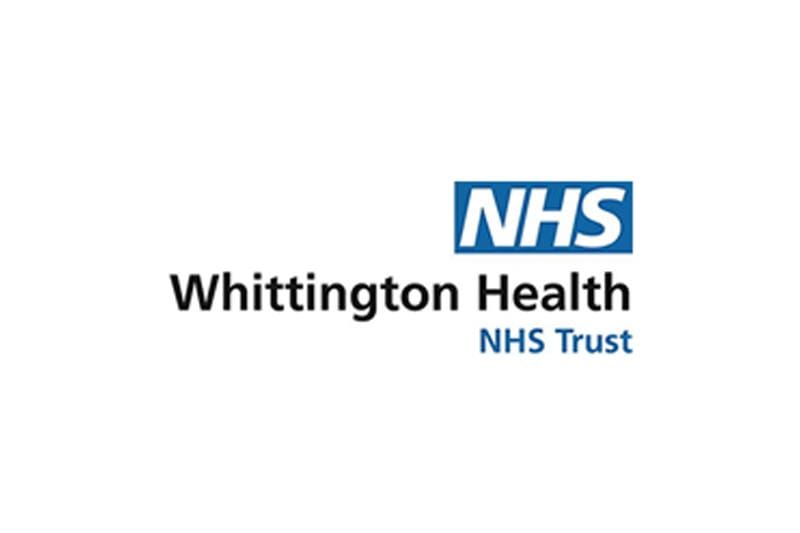
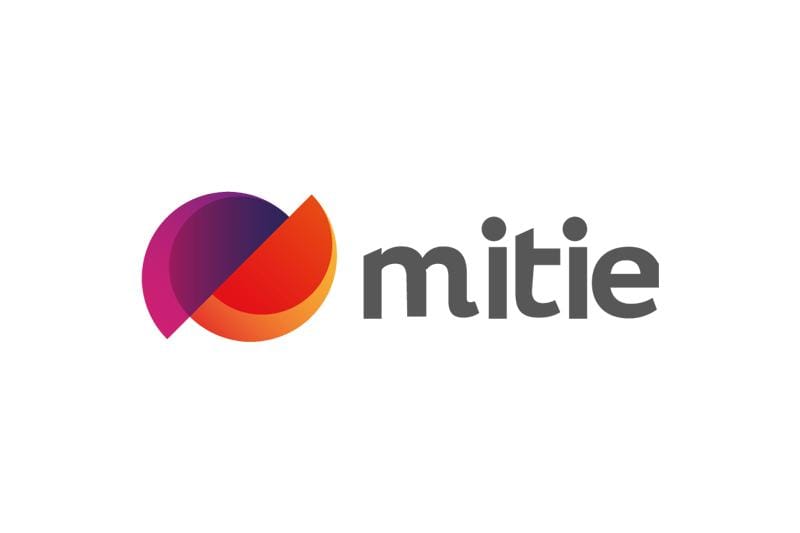
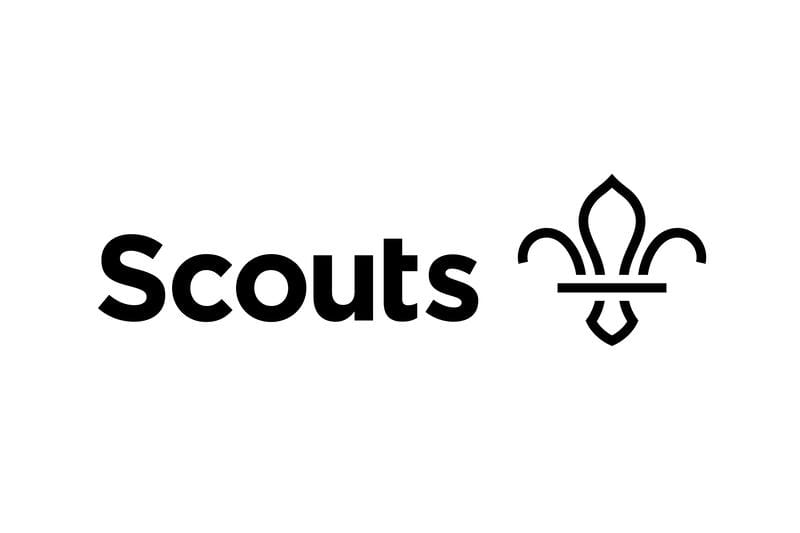

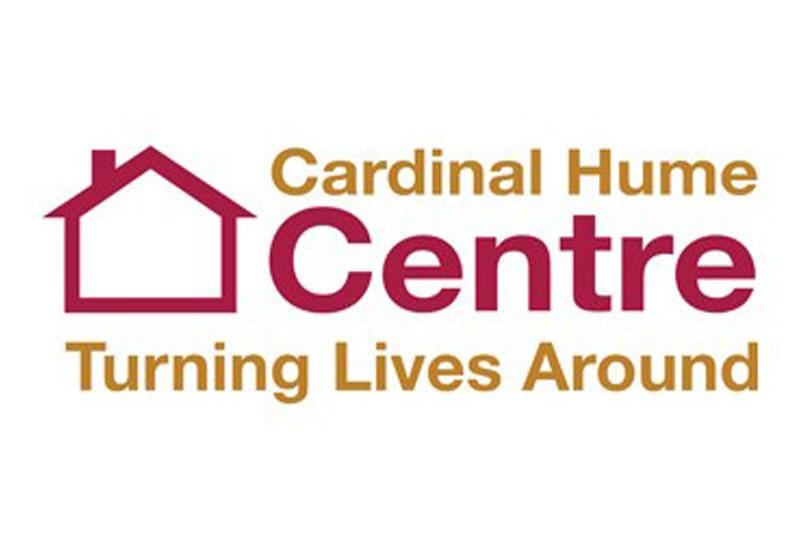
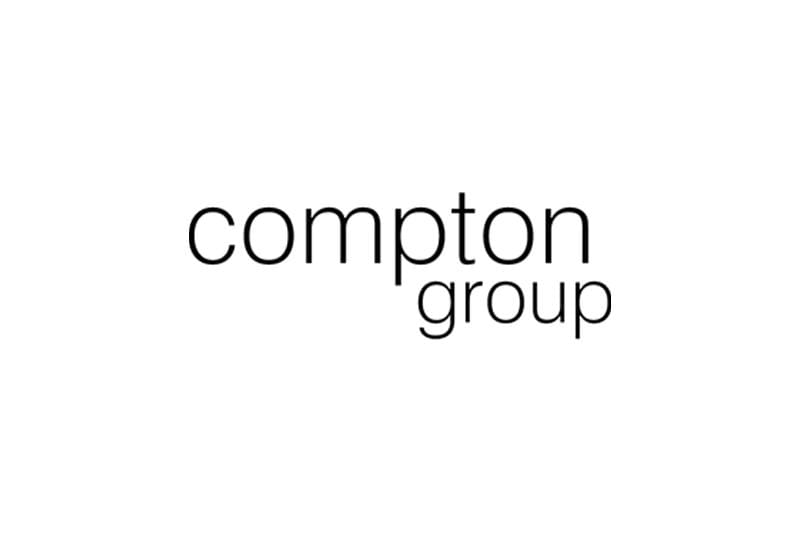
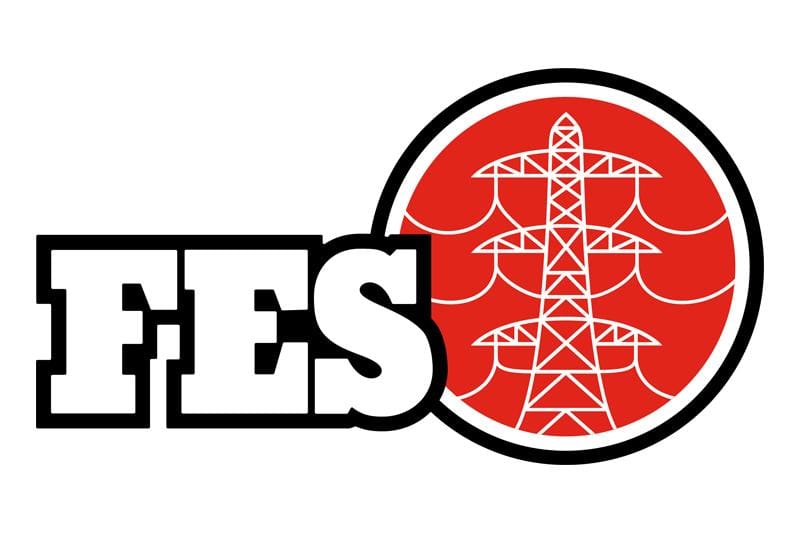
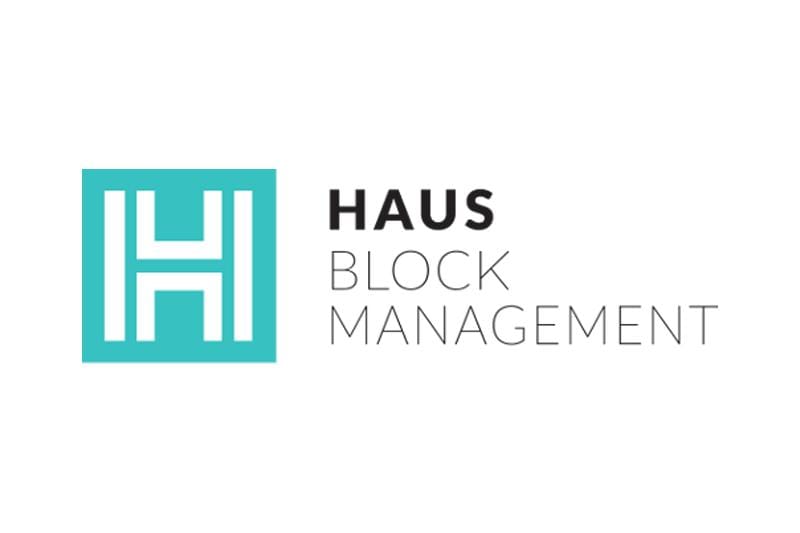
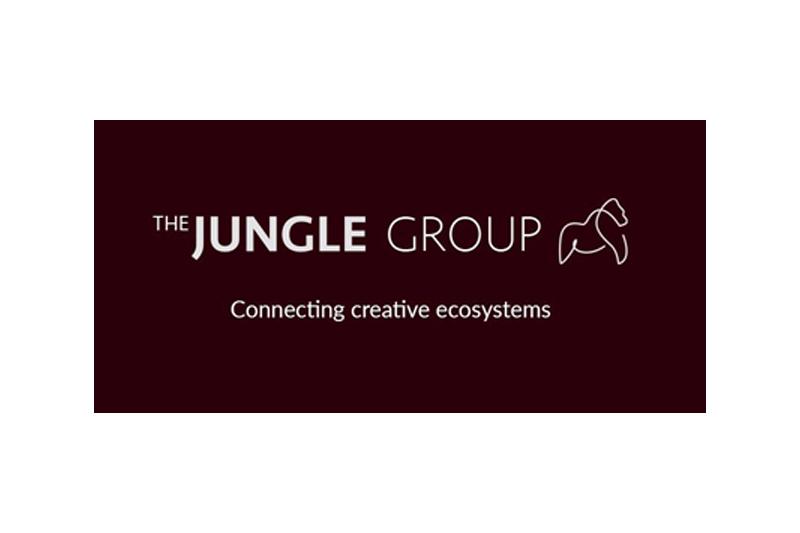
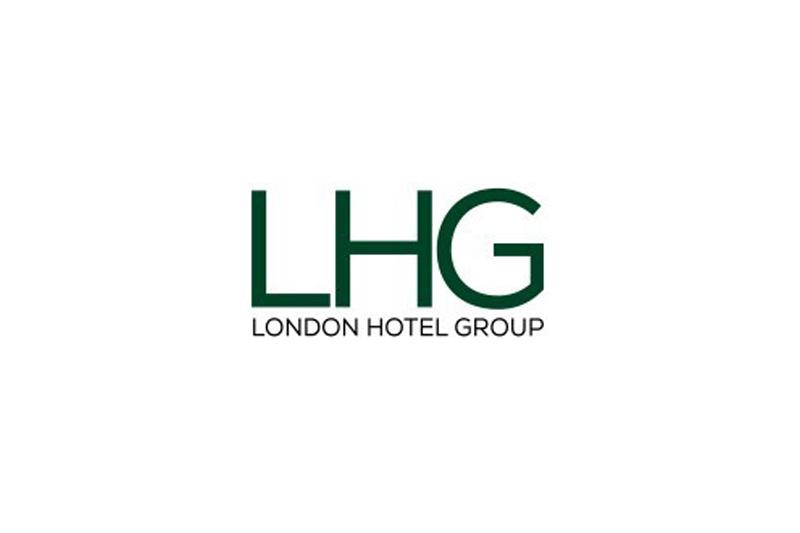
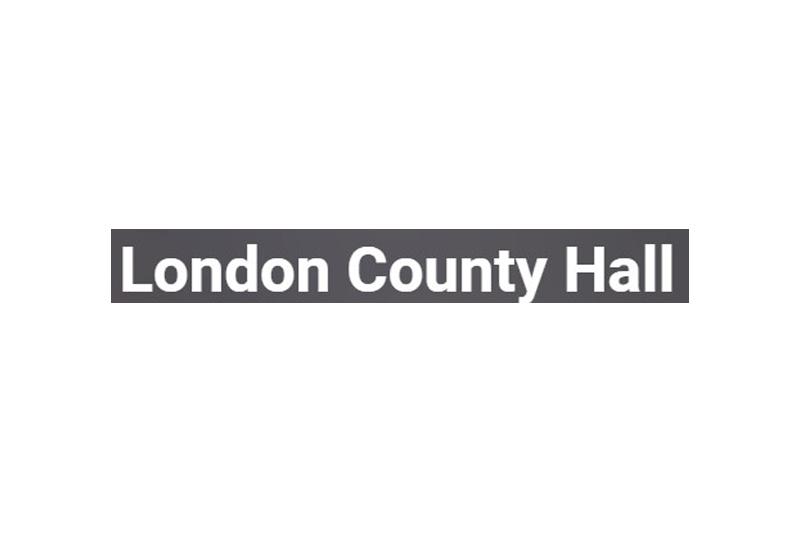
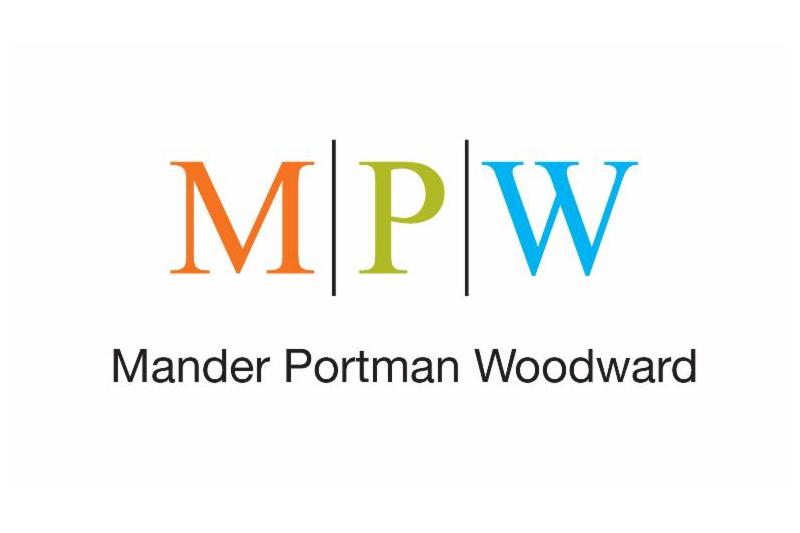
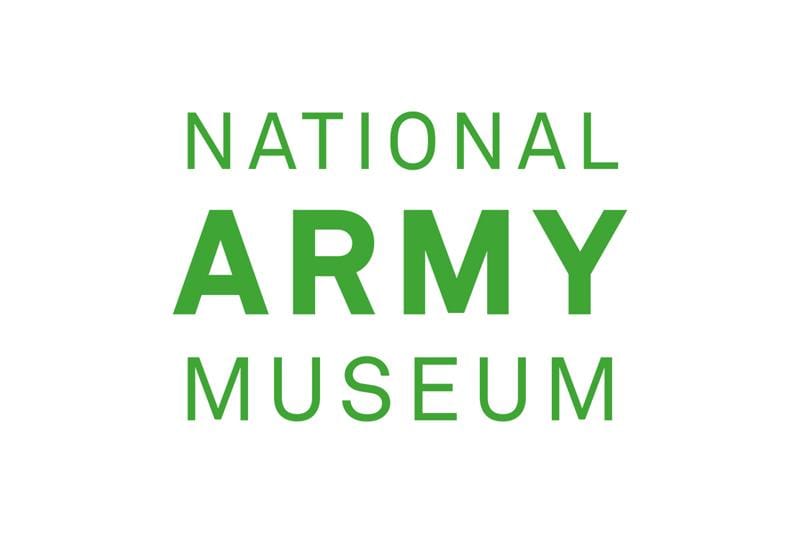
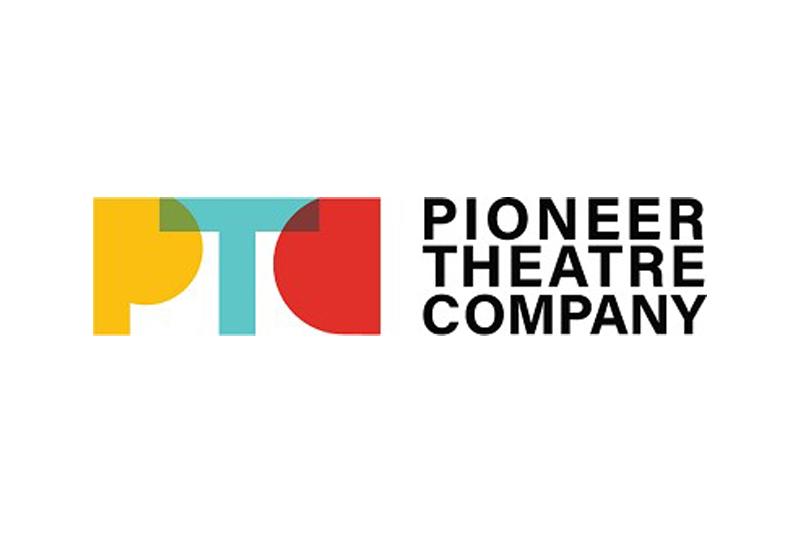
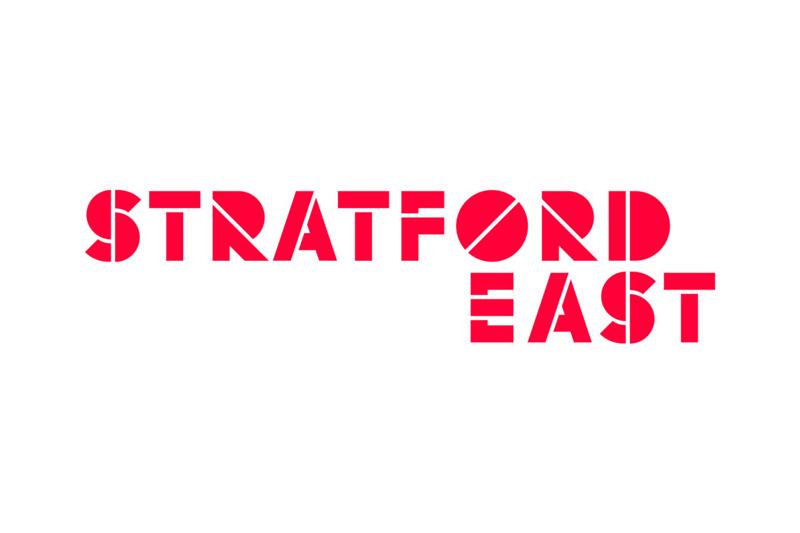
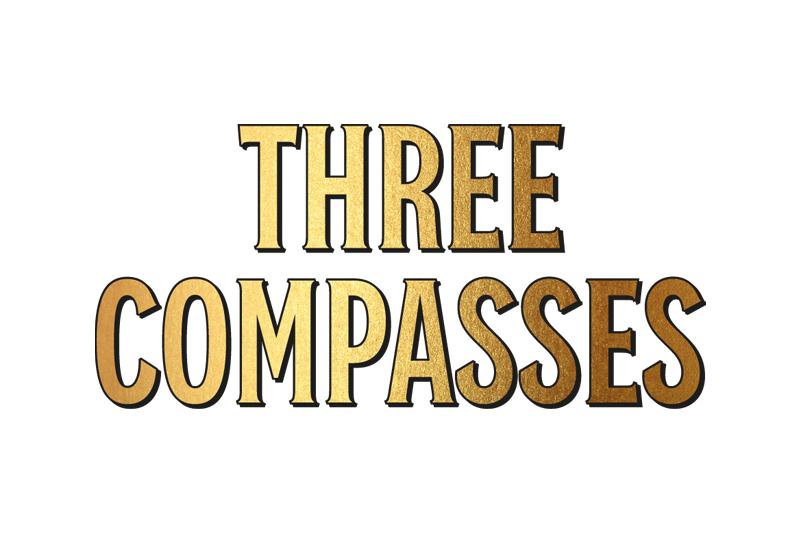
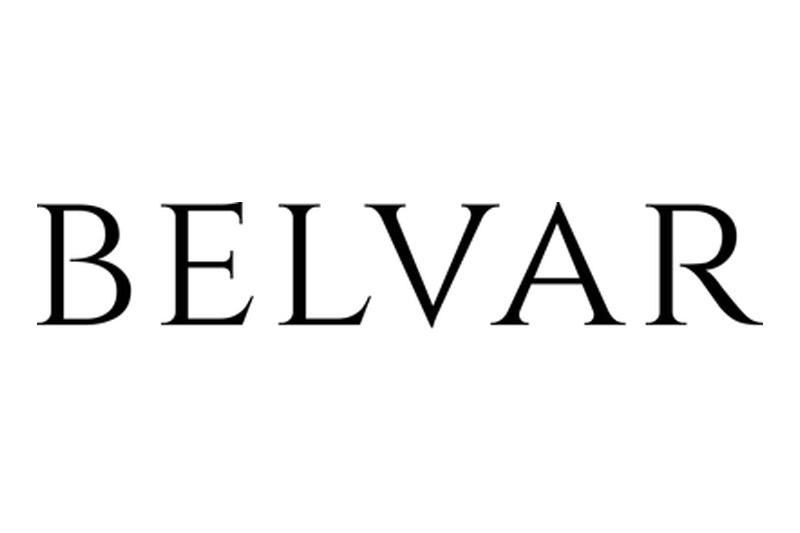
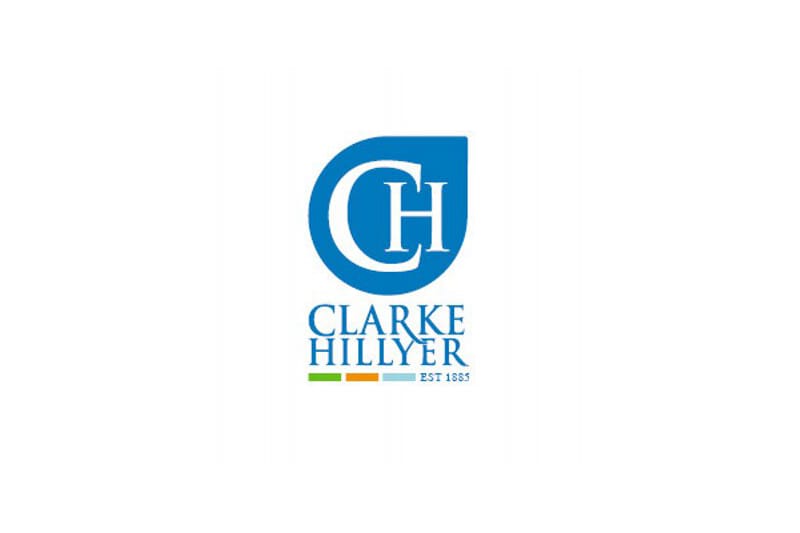
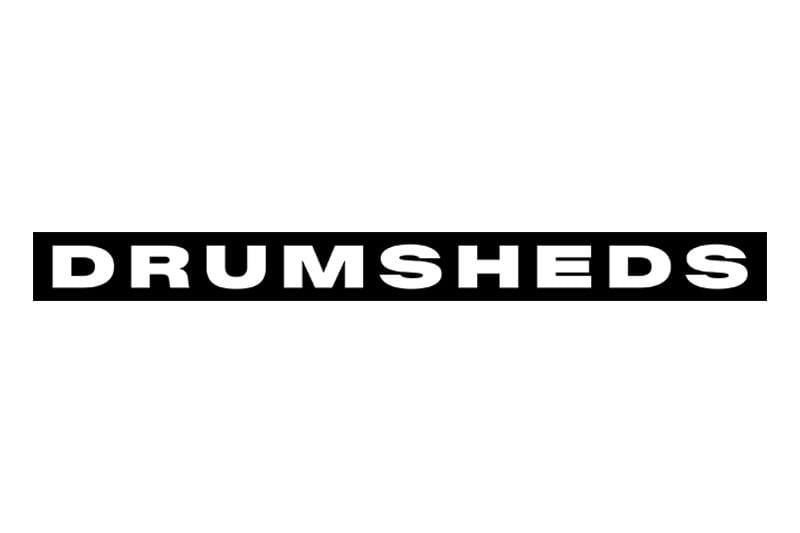
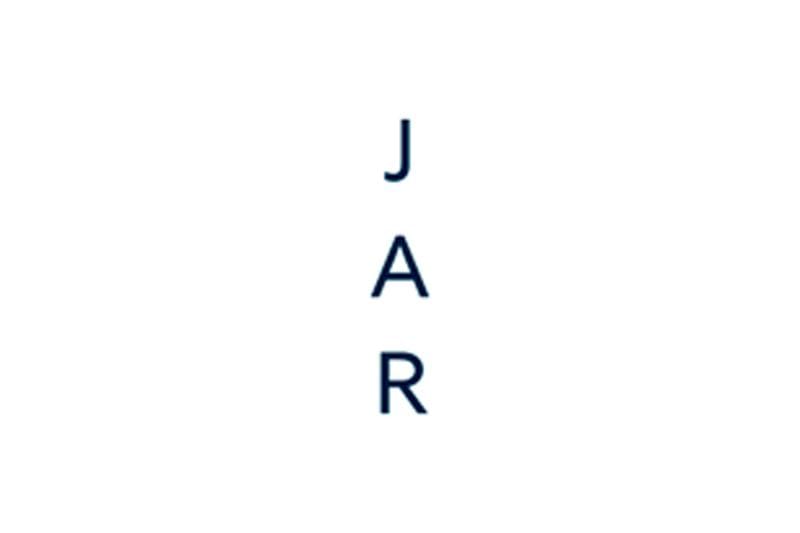
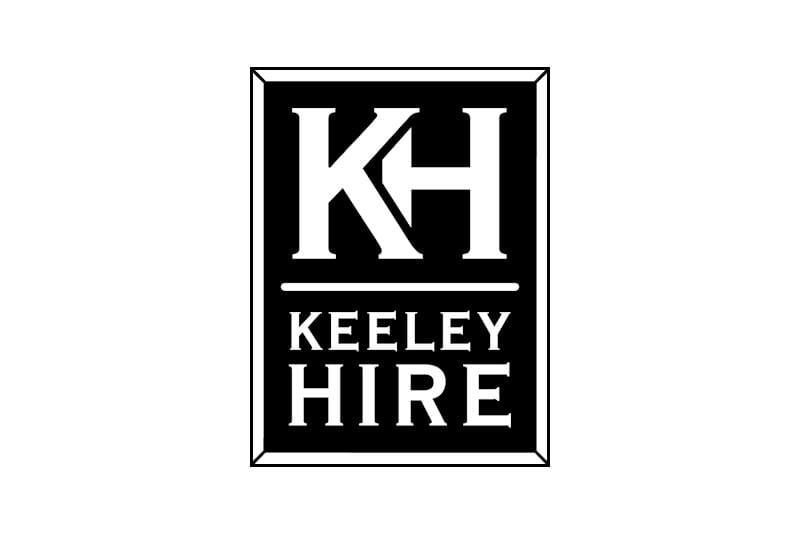
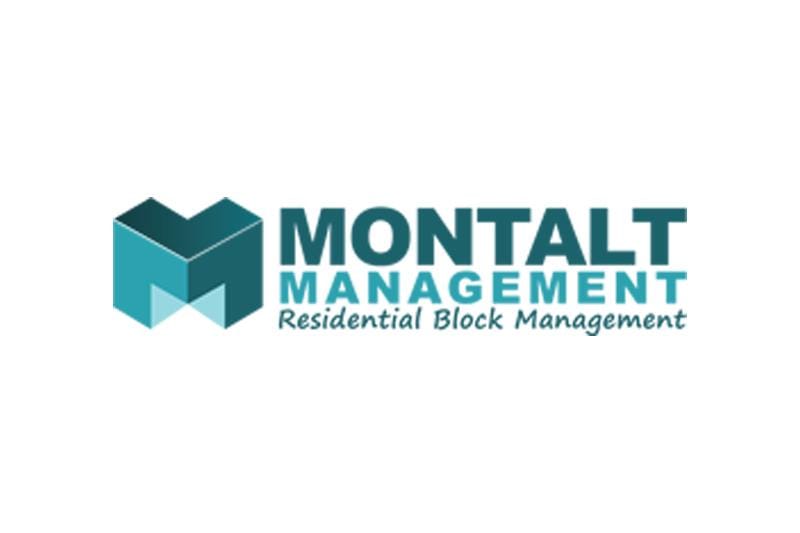
Emergency Lift Breakdown & Callout Services FAQ’s
What is PUWER?
- Suitable for the use it is intended for
- Regularly maintained and in a safe condition
- Regularly inspected for any signs of wear to ensure the equipment is functioning correctly and fir for purpose.
- Is installed correctly
- Adequate information and training on usage has taken place
- Health and Safety measures are abided to and equipment is appropriately labelled.
Other forms of vertical transportation, which have been installed in public places primarily for the use of customers outside of the working environment, must meet the requirements of all product supply legislation and have been designed in a safe manner. Stair lifts and mobility lifts are covered under the Supply or Machinery (Safety) Regulations 2008 and conventional passenger lifts must abide by the requirements of the Lifts Regulations 2016.
Here at VM Elevators the protection of our engineers, our clients and the general public from any risk is of the utmost importance. Before we undertake any work, due diligence is performed and thorough risk assessments are conducted to ensure the correct provisions are in place. We hold full membership to The Lift and Escalator Association and strongly comply to their guidance and the completion of their annual Safety Charter regulations. Any work that’s being conducted can present elements of risk to those persons directly or indirectly involved. We are also members of the British Safety Council. Legislation exists to ensure the correct parameters are in place to secure the welfare of the persons at work and others and protecting them via provisions. Our engineers are all armed with training, BS 7255 – Safe Working on Lifts and the ‘Site Safety Handbook’ – published by LEIA and updated periodically and safety refreshers to ensure they abide by the Acts within the HSW Legislation. We also conform to The British Standard BS 7255 Code of Practice for Safe working on lifts. Our commitment to integrity and transparency ensures you are informed about every aspect of the repair process upfront. We prioritise customer satisfaction through open communication and a deep understanding of each client’s unique needs. Our turnkey solutions mean we handle everything in-house, providing you with comprehensive services and in-house quotations without the need to source different providers. Additionally, our digitised worksheets provide real-time updates, allowing for faster turnaround and enhanced service efficiency. With VM Elevators, you benefit from our unwavering dedication to safety, sustainability, and the highest standards of service, making us the preferred choice for all your lift and escalator repair needs. Learn more about VM Elevators hereWhat is SAFed?
The Health and Safety at Work etc. Act 1974
What are the common reasons for lift and escalator breakdowns?
How do I know if my lift and/or escalator needs repairs?
What should I do if my lift and escalator stops working?
Can VM Elevators repair all types of models?
How long does it take to repair an lift and escalator?
Are emergency repair services available?
What is the cost of lift and escalator repairs?
How can I prevent frequent lift and escalator repairs?
Visit our lift maintenance page for more info.
Can outdated lift and escalators be repaired or should they be replaced?
Why choose VM Elevators for your lift and escalator repair needs?
What areas does VM Elevators cover for lift and escalator repairs?
Does VM Elevators have a good safety record?
What accreditations does VM Elevators hold?